Rensselaer strongly encourages new laboratories to schedule a visit with Environmental Health & Safety (EHS) to evaluate new laboratory spaces to identify potential hazards, methods to reduce risks, safety training, and proper personal protective equipment. The purpose of the visit is to foster a strong safety partnership with the laboratory workers in order to protect individuals and the facility, and to help ensure regulatory compliance.
Before a new experiment, procedure or project is developed in the lab, a risk assessment should be performed. A risk assessment provides information about establishing proper procedures, enhancing safety practices, and allows for all laboratory workers to be properly trained.
When assessing your lab, consider the full range of safety, health, and environmental hazards, from machine safety to physical hazards to chemical and biological exposures. Be sure to consult the Chemical Hygiene Plan for standards in safe work practices and discuss your findings with anyone who will perform the experiments or tasks being considered.
The risk assessment tool provides a framework for risk assessment complimenting the process laboratory workers already use to answer scientific questions.
Laboratory workers conducting work in Rensselaer laboratories must complete Laboratory Safety Training provided by Human Resources in Percipio.
Additional training provided by EHS is required depending on the activities of the laboratory worker. Such training may include laser safety, radiation safety, biosafety or other topics. The training sessions provided by EHS give an overview of universal safety procedures for working with hazards that may be encountered in the lab. It is generalized and does not cover safety items specific to the hazards present in each lab.
Principal Investigators and lab supervisors must ensure members of their labs are trained in the safe and proper practices for the procedures and materials used and any lab‐specific safety measures they may take to protect themselves from exposure to hazardous materials, including the location and use of emergency equipment.
Additional training may be necessary as new equipment, materials and/or processes are introduced.
Effective controls protect employees and students to avoid injuries, illnesses, and incidents, minimize or eliminate safety and health risks, and help employers provide workers with safe and healthful working conditions. To effectively control and prevent hazards, Principal Investigators and laboratory supervisors should look at the hierarchy of controls established by OSHA to protect their laboratory workers. Controls should be selected that are the most feasible, effective, and permanent.
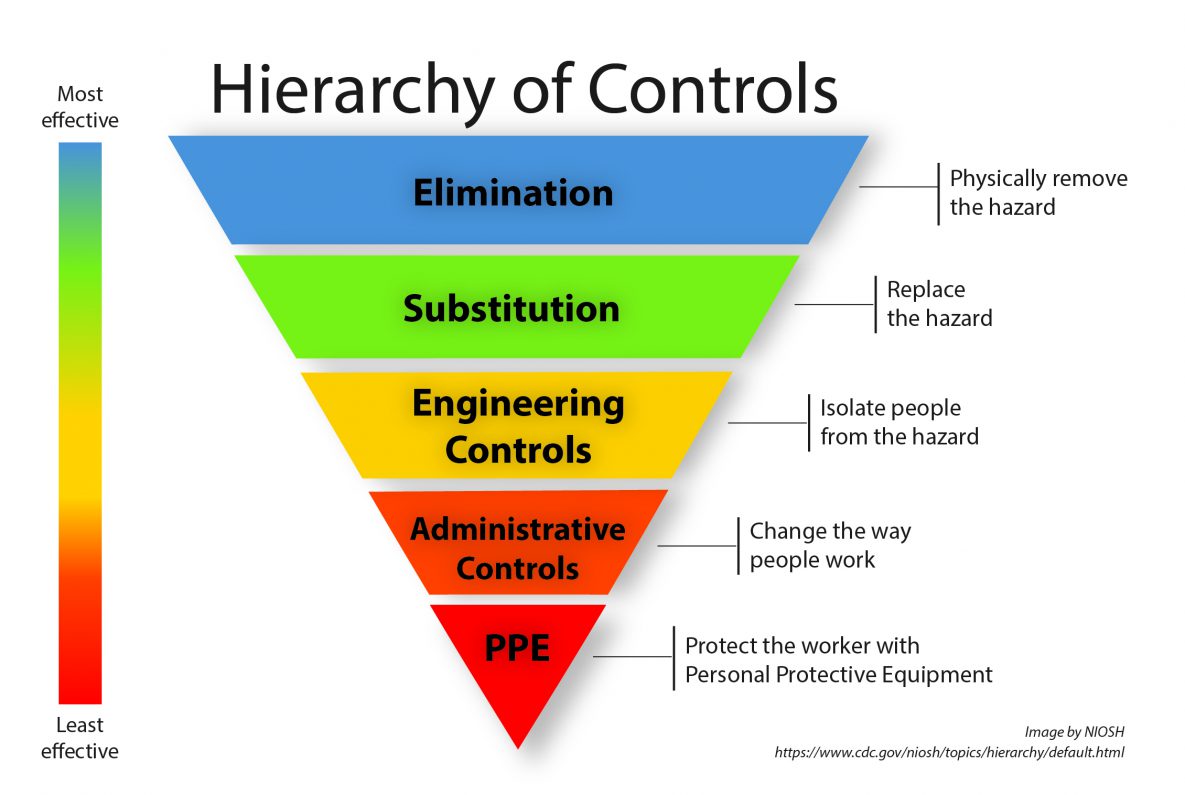
When a lab decommission is necessary, the proper disposal or transfer of hazardous materials used in laboratories lies with the Principal Investigator (PI) to ensure that all substances and equipment are safely moved, or disposed of, and the space has been appropriately decontaminated.
PIs are encouraged to consult the Rensselaer Chemical Hygiene Plan, Biosafety Program, Radiation Safety Program, and the Hazardous Waste Program, for guidance on the proper disposal of research materials. A collaborative effort between EHS and Physical Plant ensures that research spaces are vacated in an organized fashion, which enables the space to turn over to construction crews or the next occupant free from hazards.
If a laboratory decommission is needed, please fill out the laboratory decommissioning form and consult the laboratory decommissioning guidelines for standardized processes, strategies, and validation methods for screening and characterization of hazardous materials, proper decontamination of workspaces, and compliance with hazardous waste regulations. This process is used whether the lab move is within the Institution or to another off-campus location.